IRONBOLT for Retail
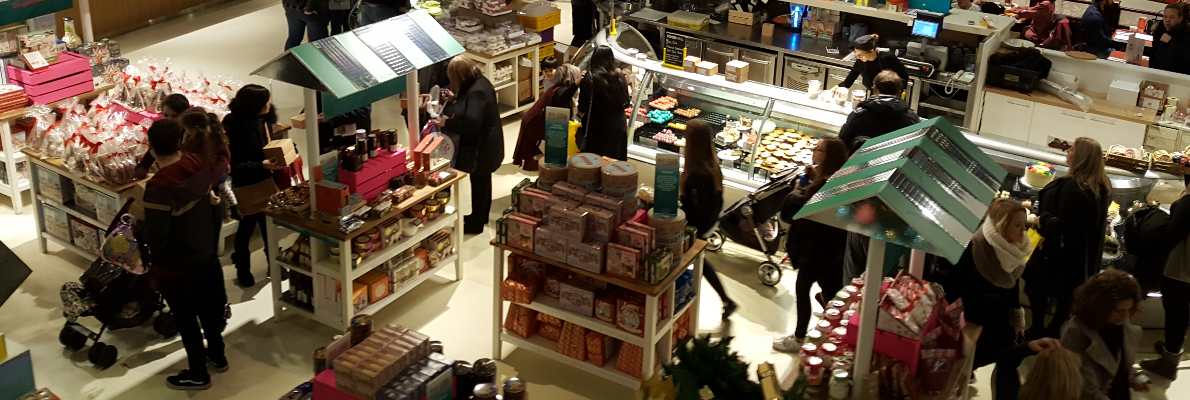
RFID Stocktaking
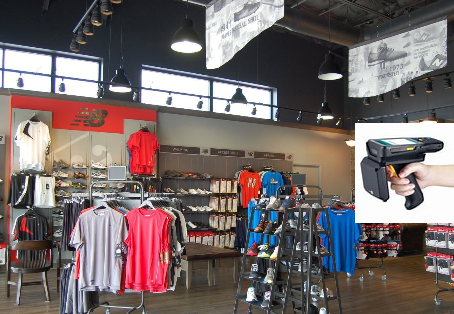
With our RFID Stocktake application, stocktakes are quick and accurate. When it only takes minutes to stocktake a full store or warehouse you can count your inventory as frequently as you like. This means smaller, faster and more frequent reconciliations and inventory adjustments.
The ability to seamlessly handle barcodes and RFID tags within the same stocktaking application makes our RFID Stocktaking system a unique and obvious choice for large retail organisations considering a staged adoption of RFID inventory control.
Improve your online offering and add individuality to each item of inventory, so you can know precisely which model, style, size and colour is in stock.
Designed for speed and leveraging IRONBOLT?s high performance cloud platform, RFID Stocktaking hand-held application can detect hundreds of items in seconds. The system handles regular stock counts or full stocktaking events, as often as you like. It is super fast.
The RFID stocktake system can be integrated via APIs with your existing Point of Sale, ERP or Ecommerce solution. We will work with your team to bring your existing inventory processes up-to-speed with the best that RFID technology has to offer.
Customer Data Hub
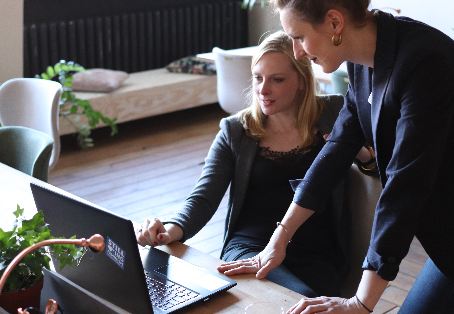
As companies extend their reach via online sales channels and platforms customer data invariably replicates across internal and third-party systems, leading to data misalignment and duplication. The more activity on the data, such as new registrations, changes in contact details and customer marketing preferences, the harder it gets to ensure that all systems have the most current details.
Our Customer Data Hub is built on the strength of the IRONBOLT data integration platform, capable of referencing customer data from your on-premise and cloud-based systems. Advanced matching and validation rules track how customer data changes across the different repositories, helping identify integration and process issues and providing a unified clean view of your data.
Space Congestion Monitoring
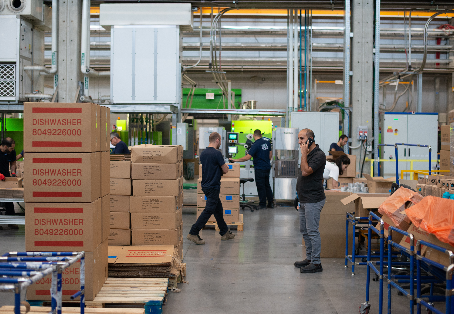
No matter how large or small, inventory storage areas experience moments when the ability to effectively process stock is impacted by space congestion. Being able to handle increasing volumes of pallets and parcels needing to be received, unpacked, put away, picked, packed, loaded and delivered becomes very challenging when your goods receiving and dispatching areas are running out of room.
Operating in a congested space invariably affects staff productivity, increases OH&S risks, causes product damages, impacts overall performance and customer satisfaction.
Using next generation photographic analysis and machine learning technologies, our space congestion monitoring solution provides a low cost, reliable tool for detecting changes in space congestion in real time, across multiple sites and inventory areas. With each monitoring sensor trained and configured to visually identify congestion tresholds, you can monitor multiple sites from the same dashboard and take action before inventory handling and storage space availability reaches critical point.